Guy Brun, fondateur de l’Ecomusée de la Margeride à Loubaresse (Cantal), nous a transmis amicalement ce reportage réalisé en 1979 chez Albert Aubagnac à Castanet-le-Bas. Nous lui exprimons toute notre gratitude pour ce document exceptionnel.
Le sonnailler de Castanet-le-Bas (Hérault)
Ethno-textes : Guy BRUN – Photographies : Claude GAL
– Printemps 1979 –
Albert AUBAGNAC, né en 1922, a appris à 17 ans le métier de fabricant de sonnailles de moutons, derrière son père, Emile Aubagnac, qui avait créé l’atelier en 1920. Emile Aubagnac est décédé en 1966 et Albert continue à fabriquer de nombreuses variétés de sonnailles qui sont expédiées dans toutes les régions pastorales de France. Il est aidé dans ce travail artisanal par sa femme, Eliette, et ses deux fils, Guy et Michel, lorsque celui-ci n’est pas à l’école.
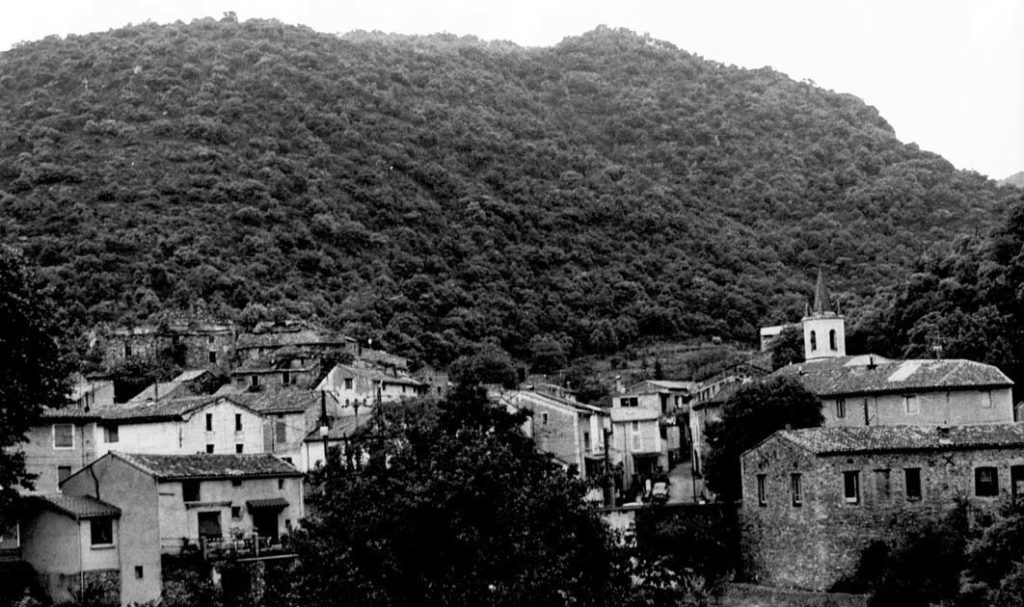
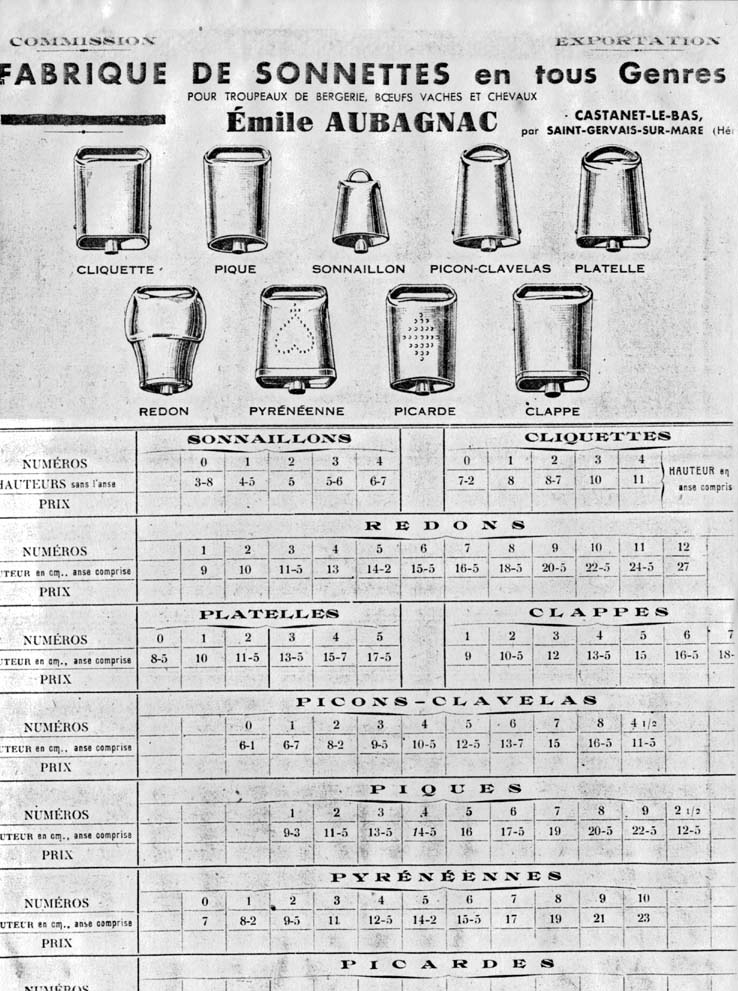
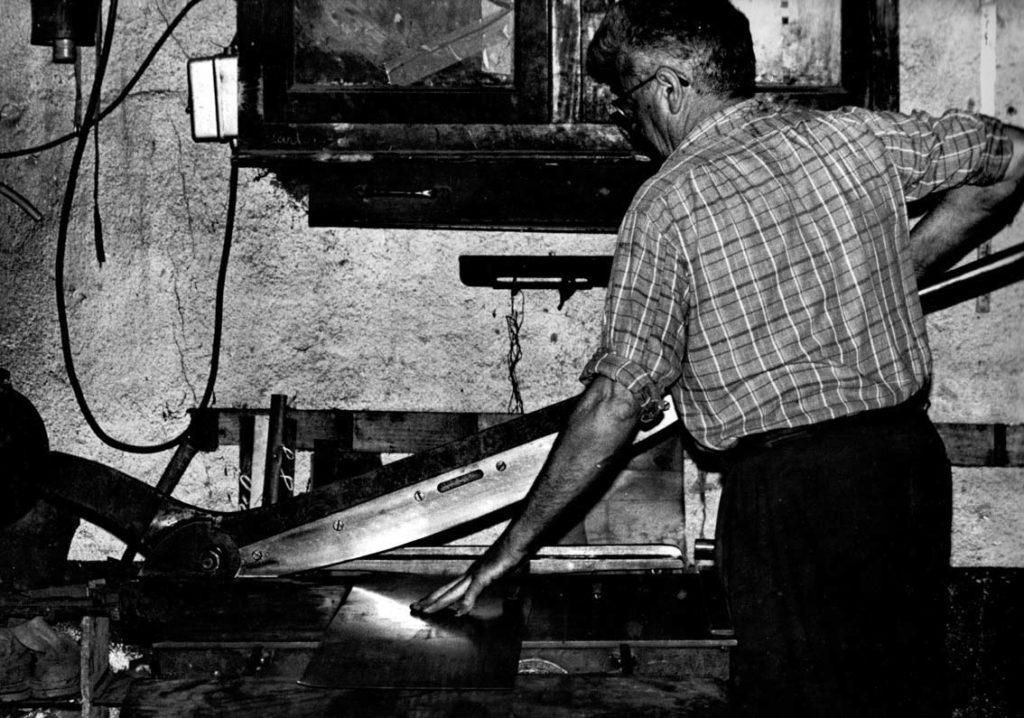
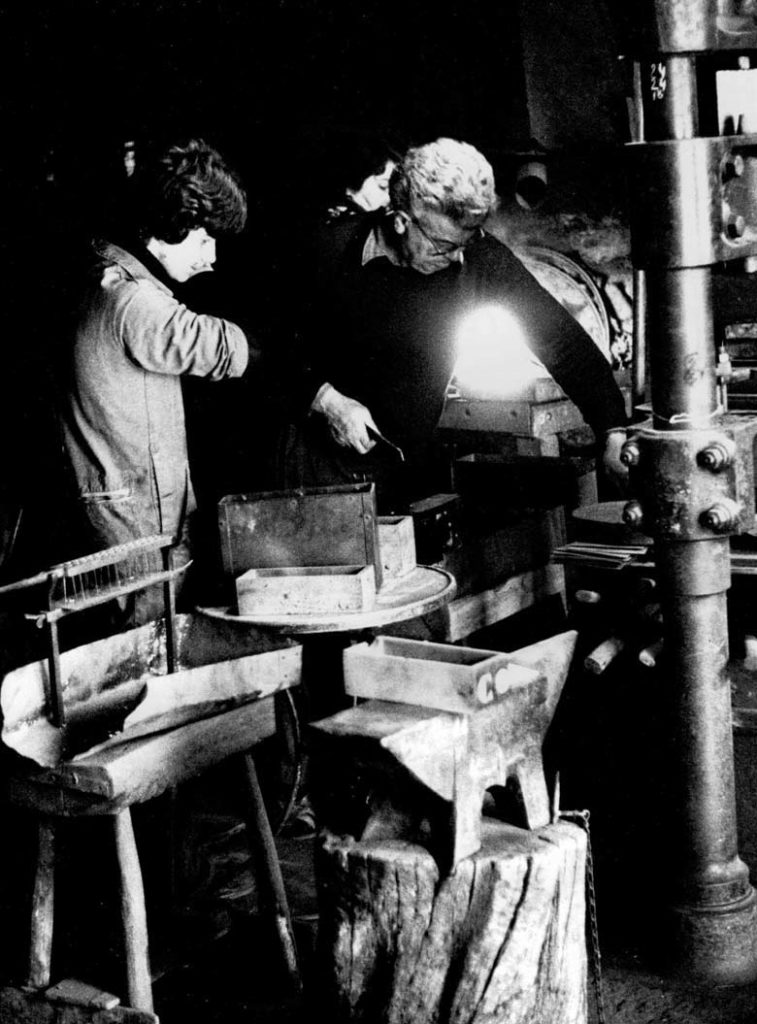
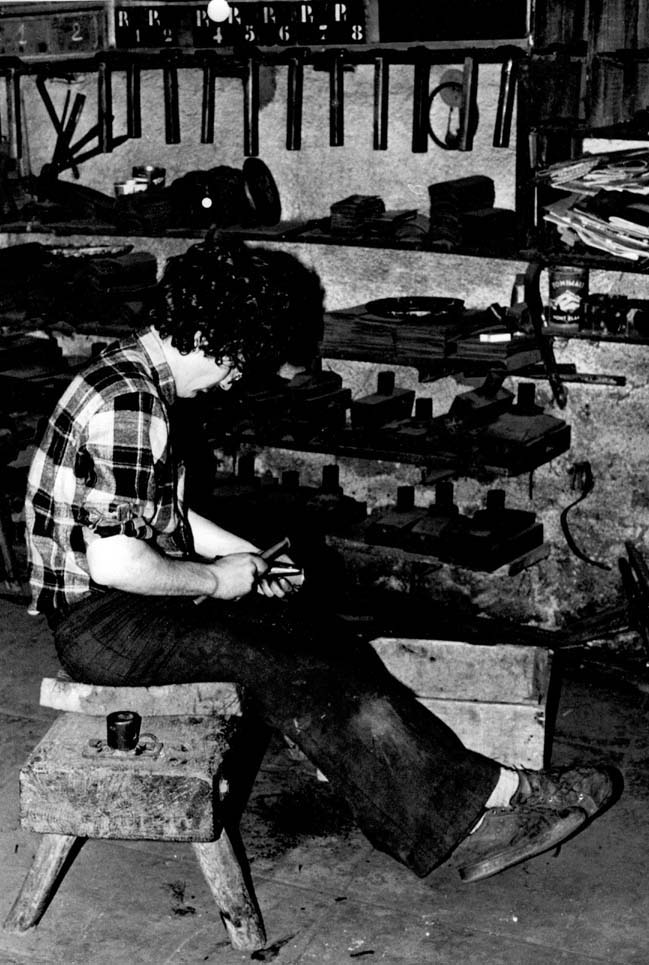
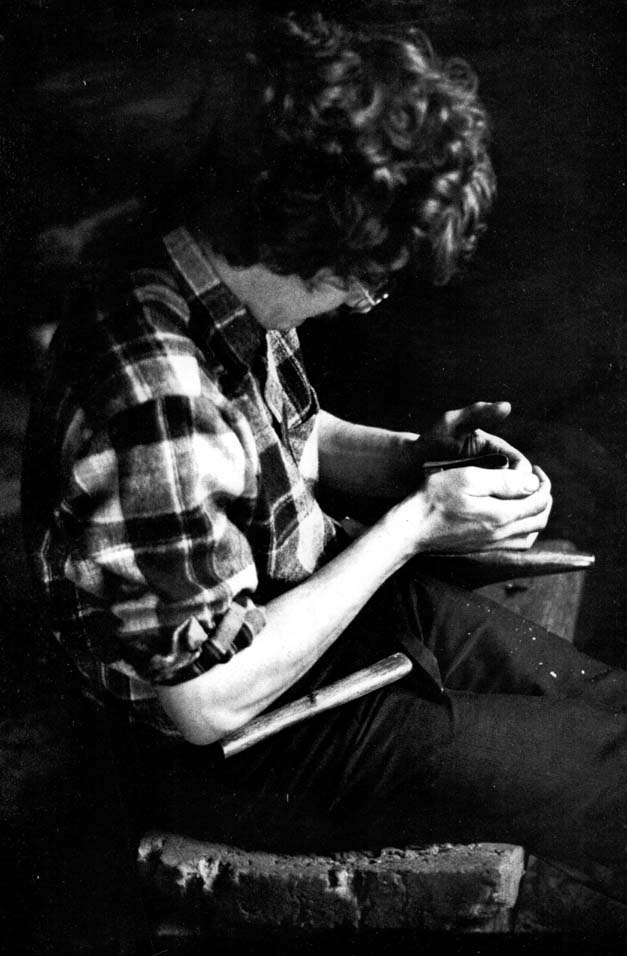
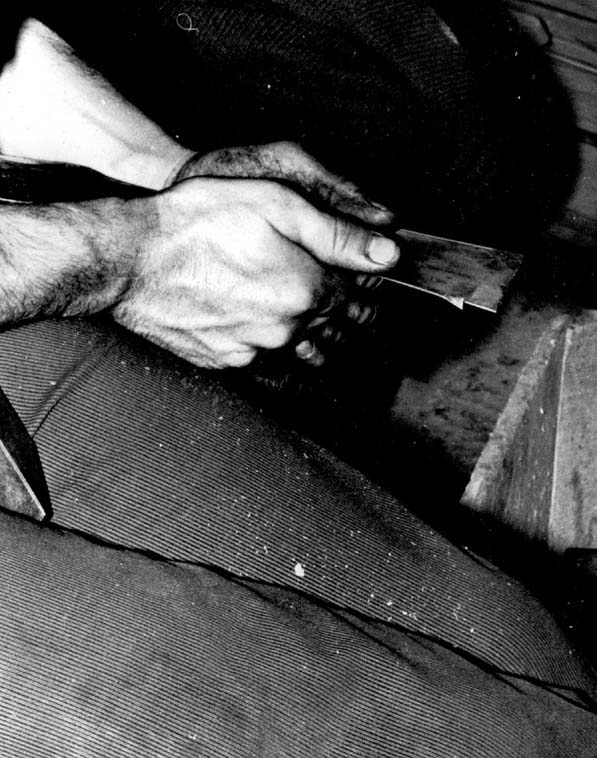
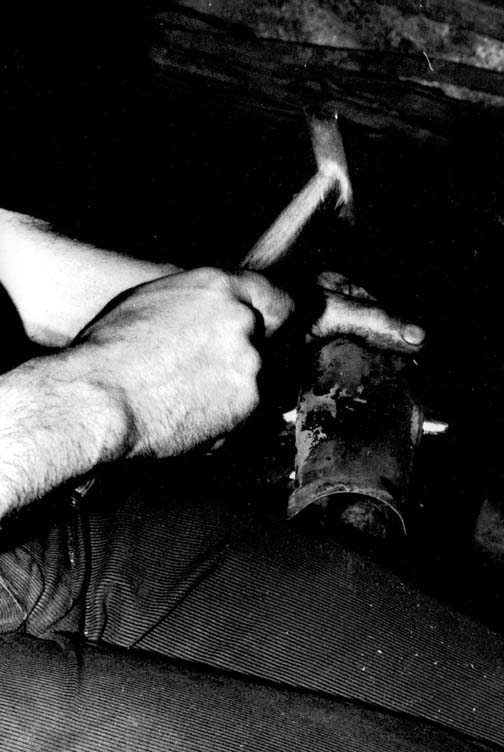
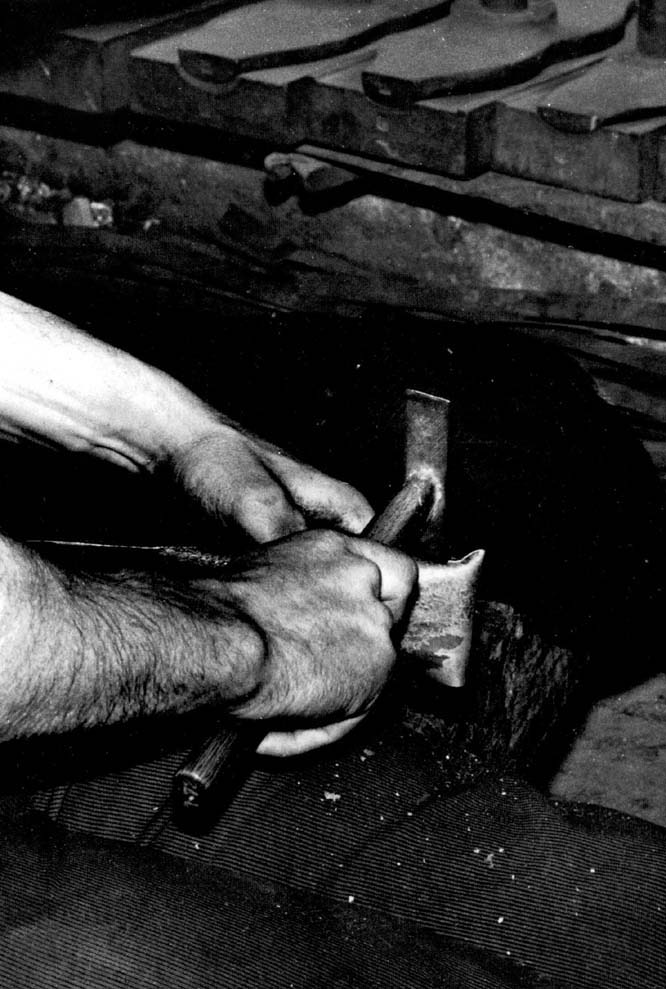
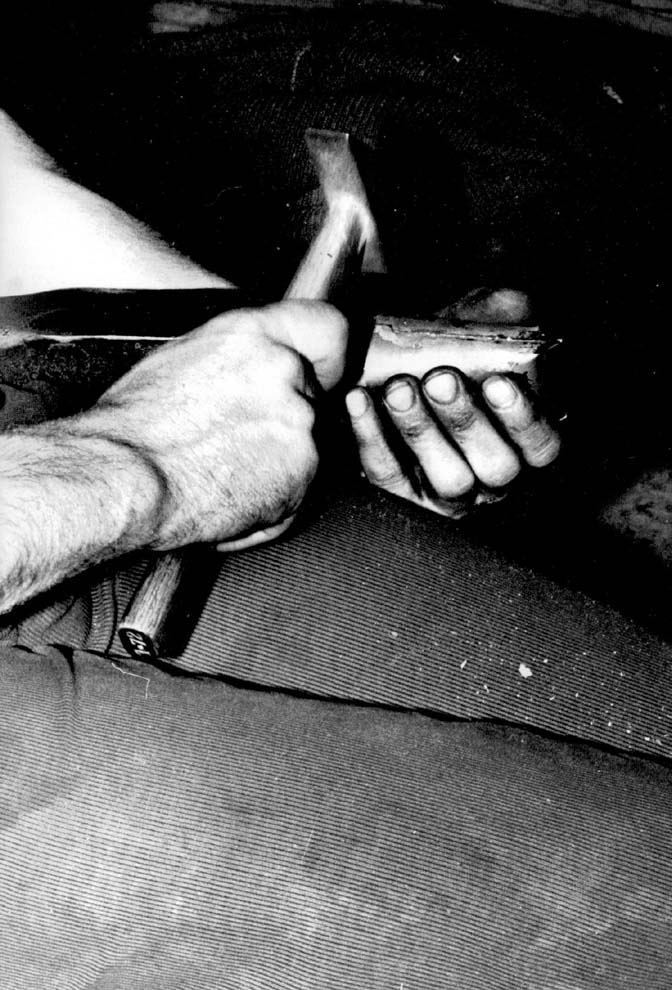
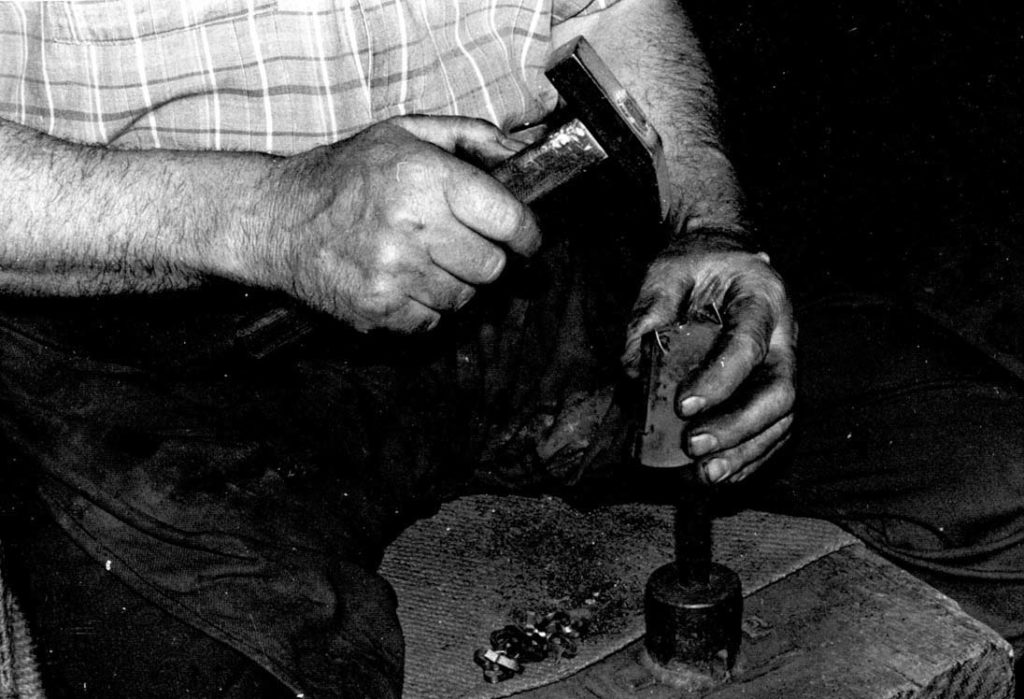
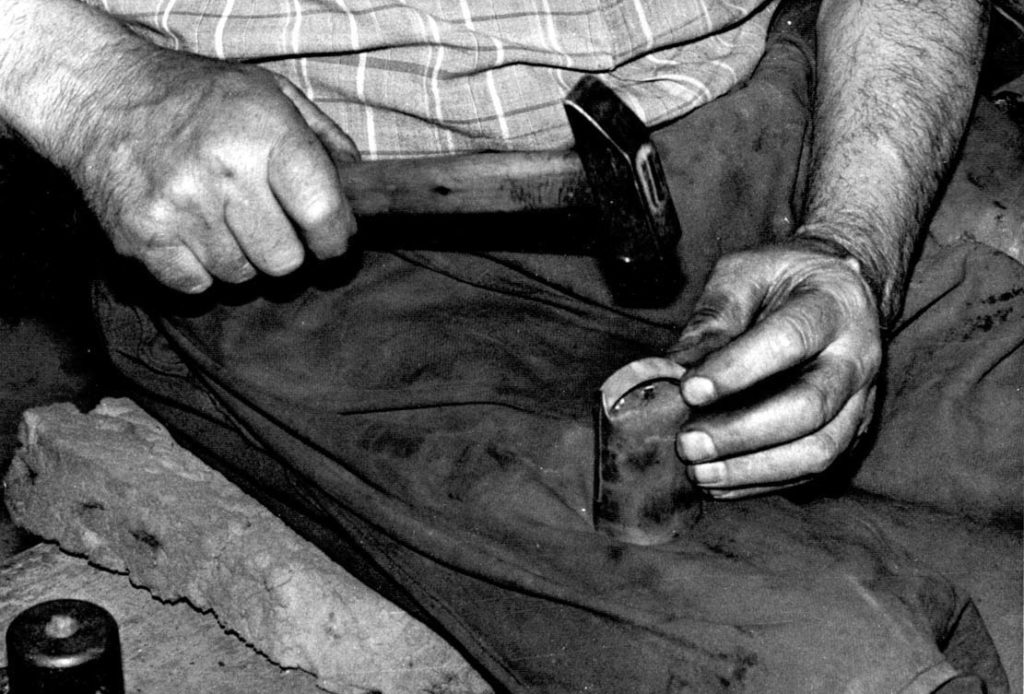
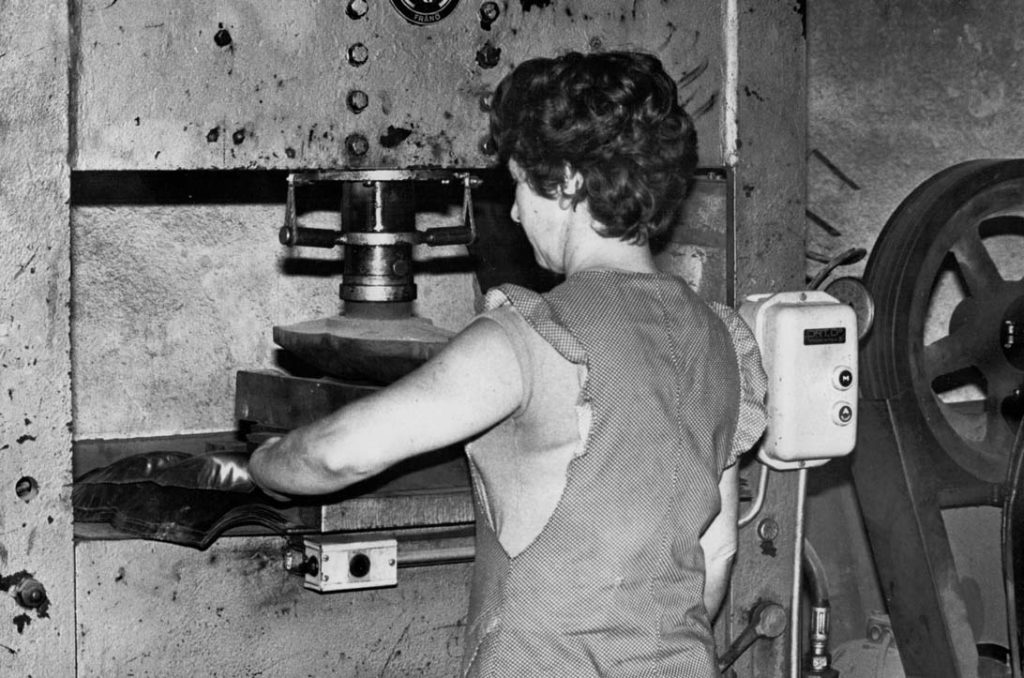
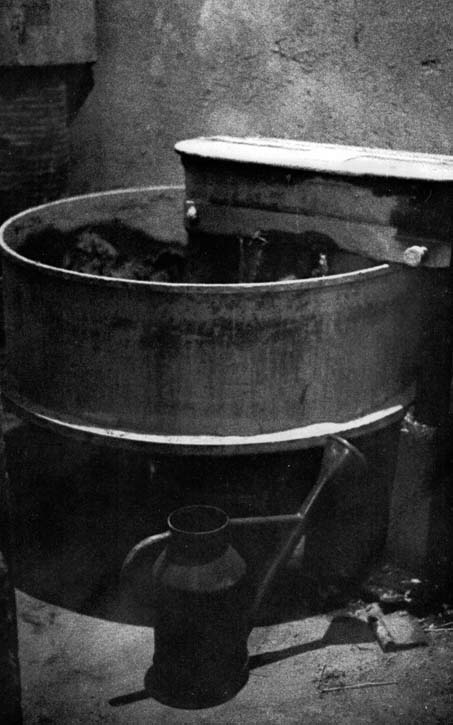
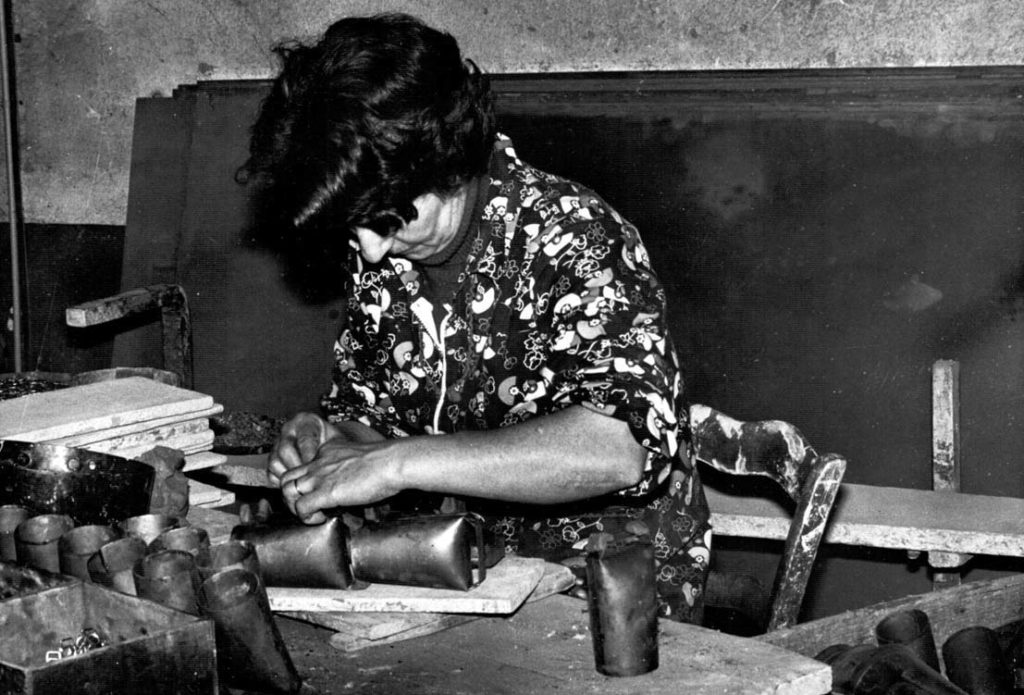
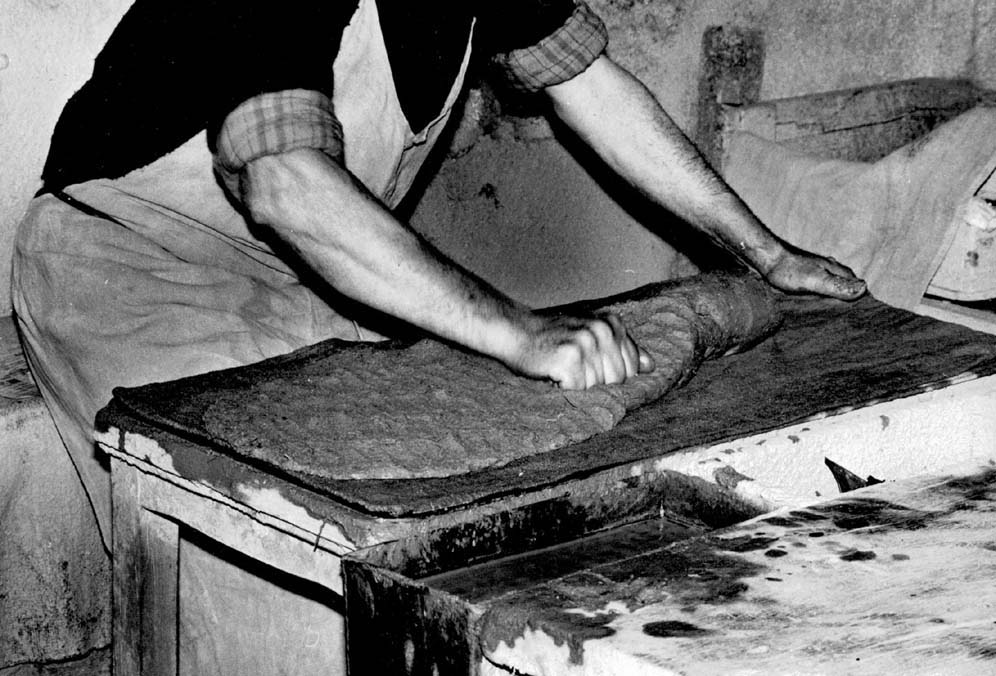
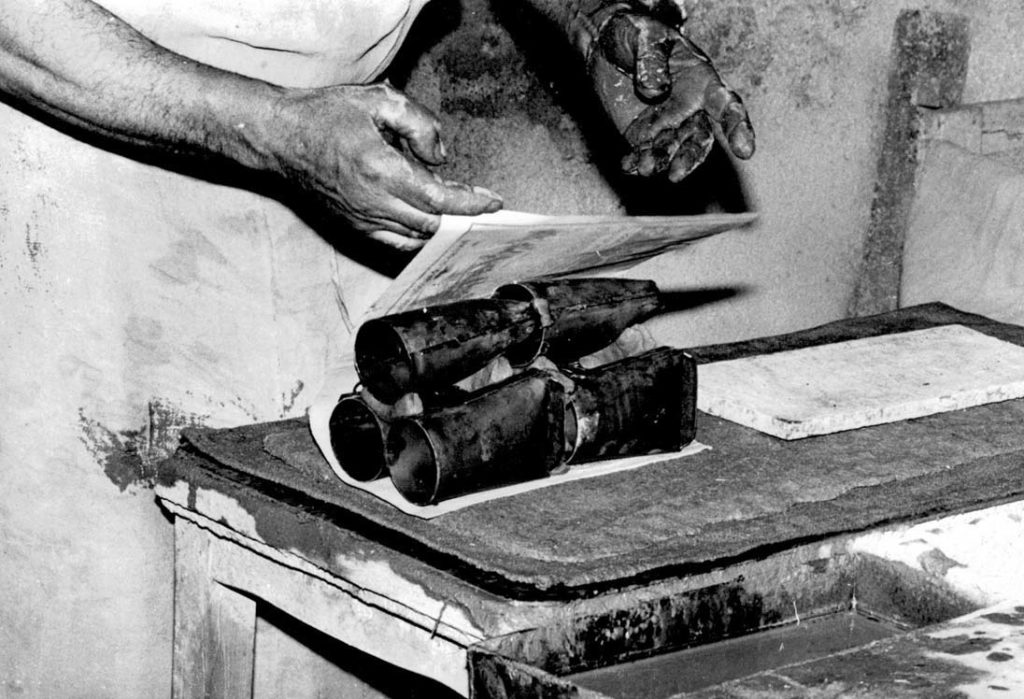
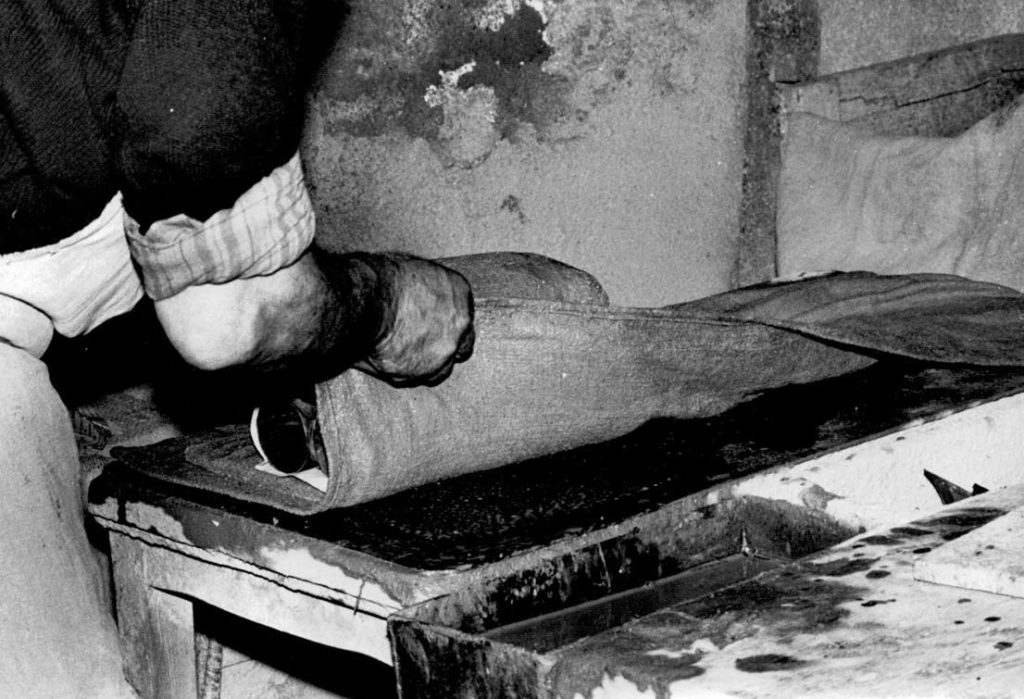
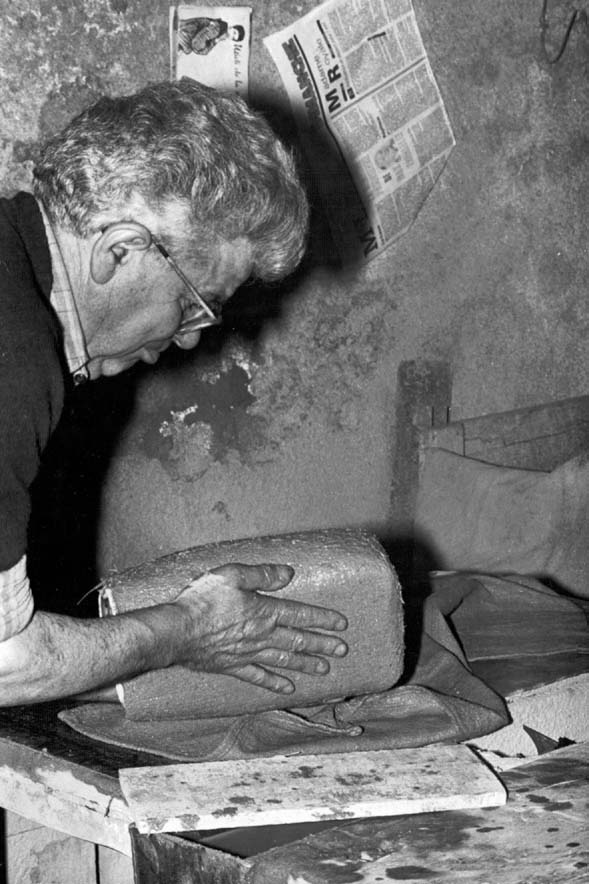
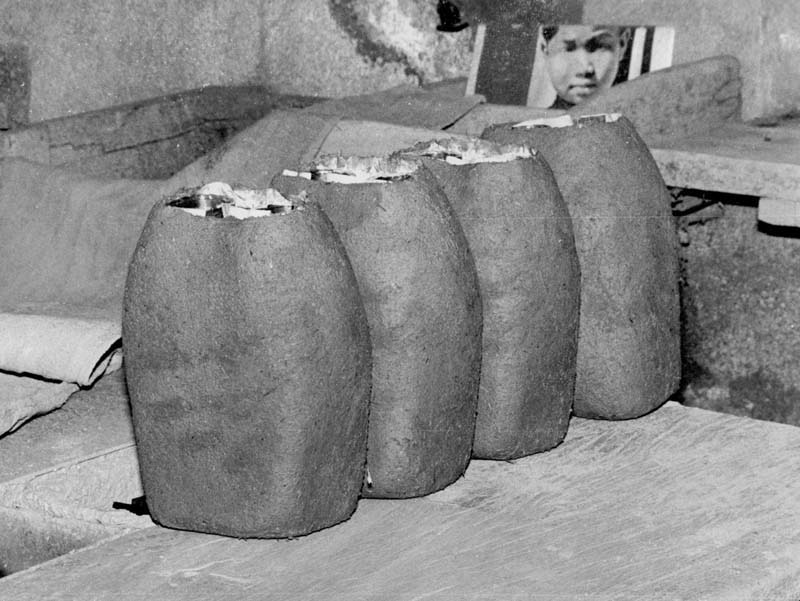
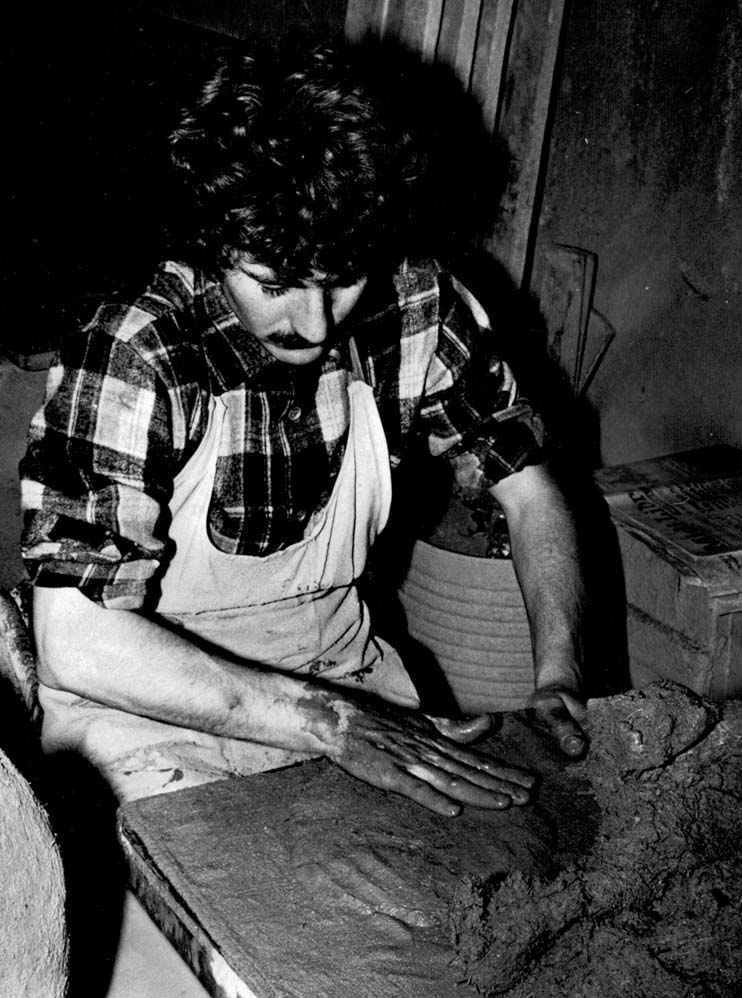
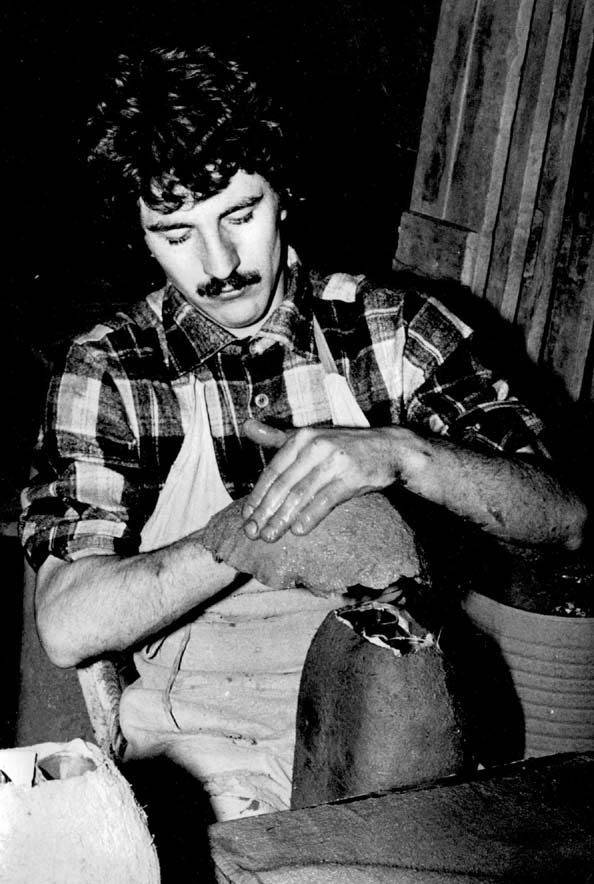
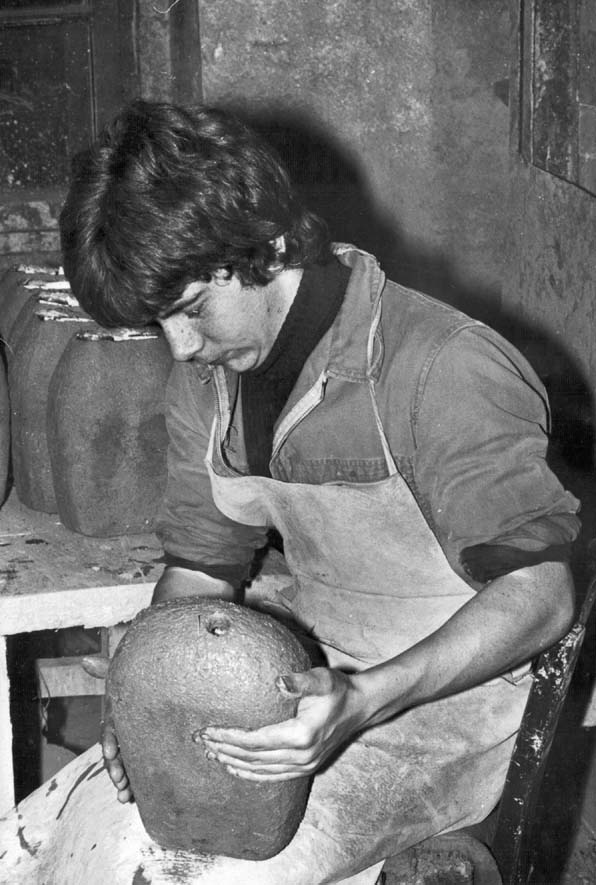
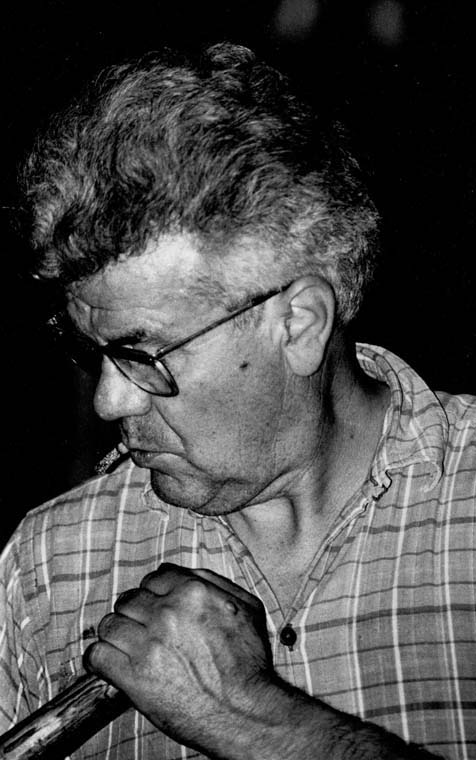
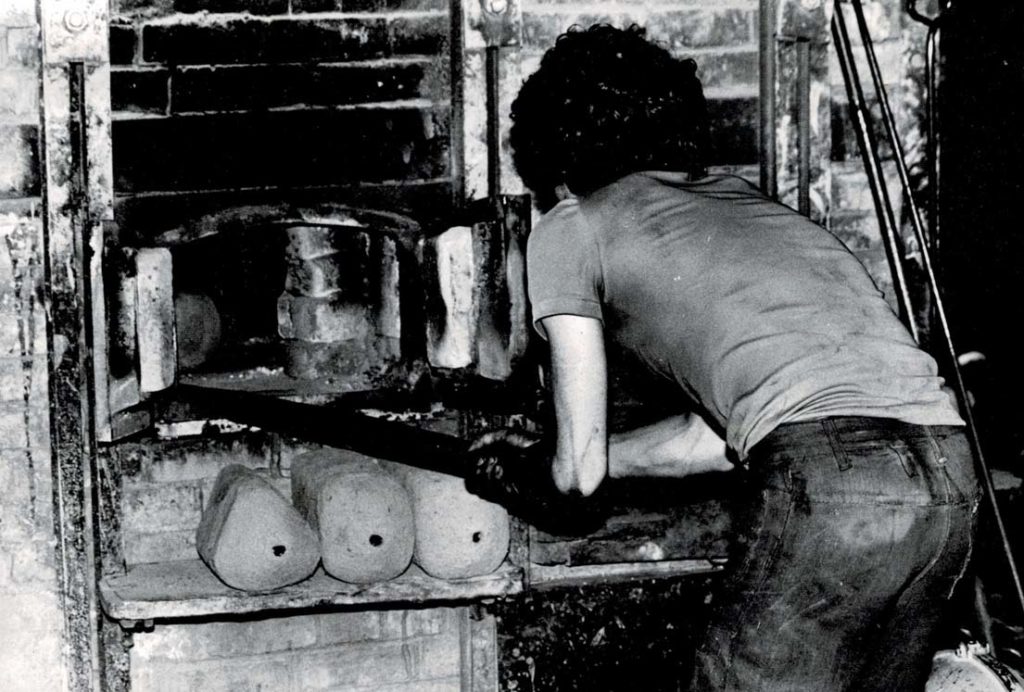
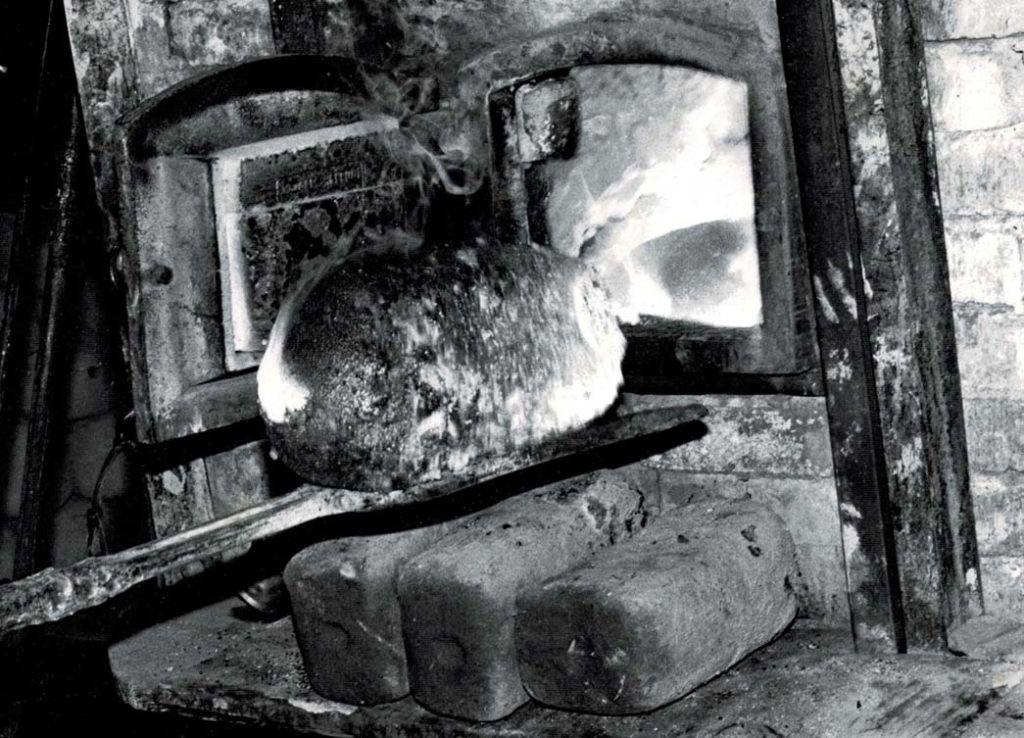
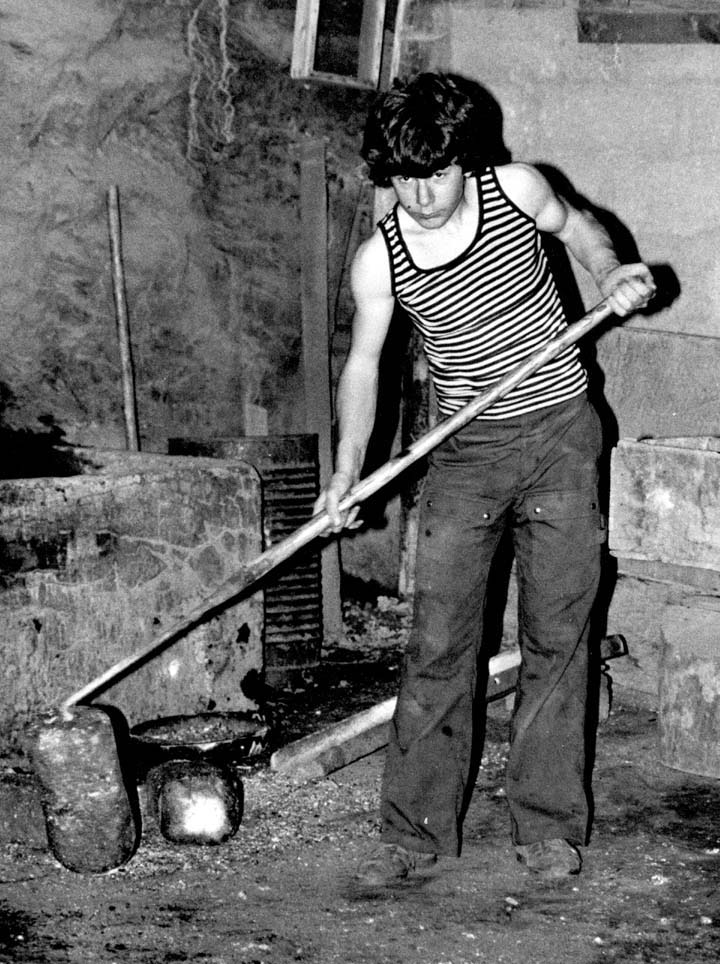
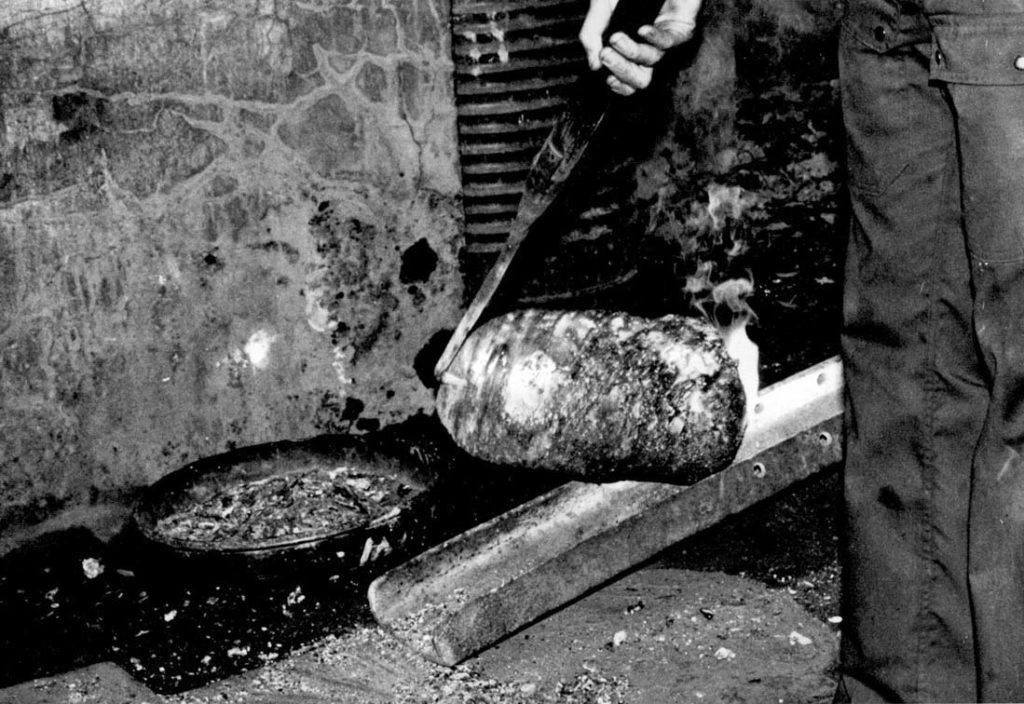
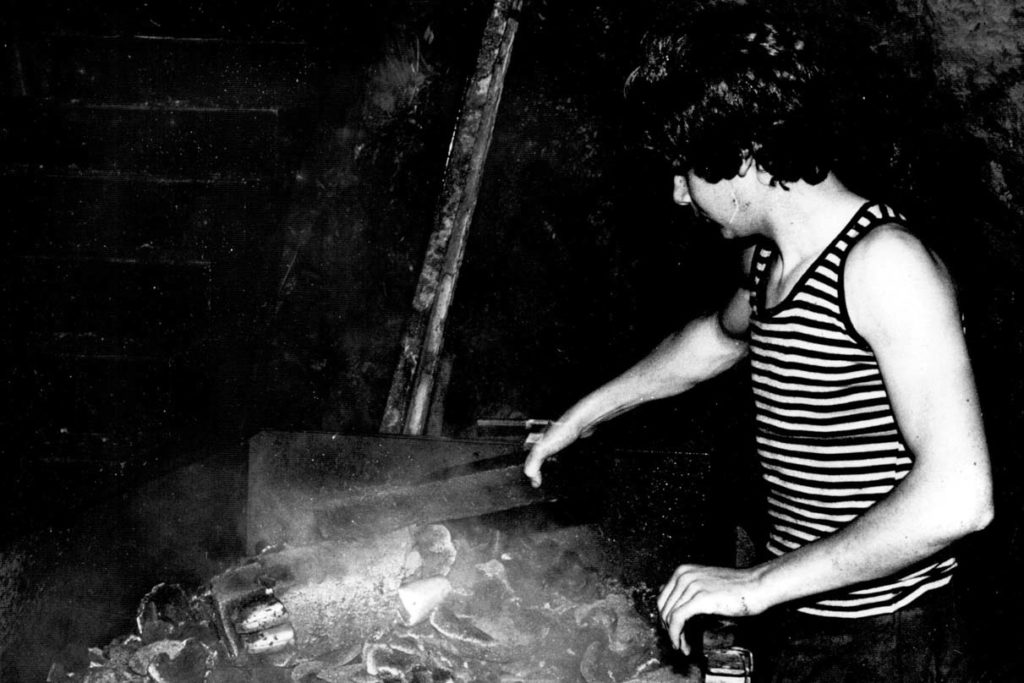

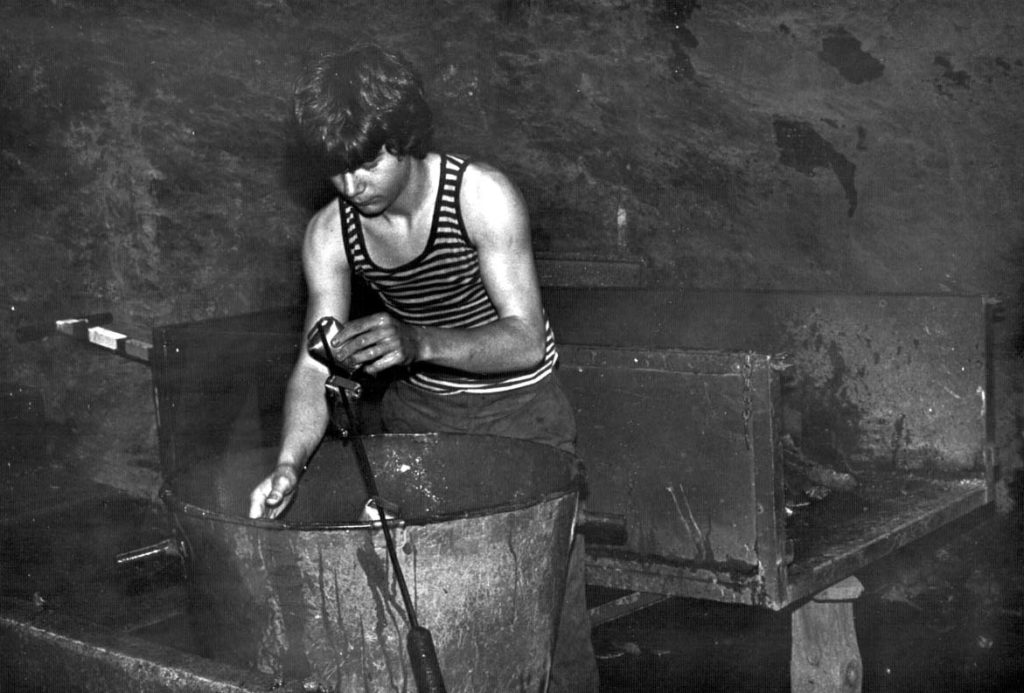
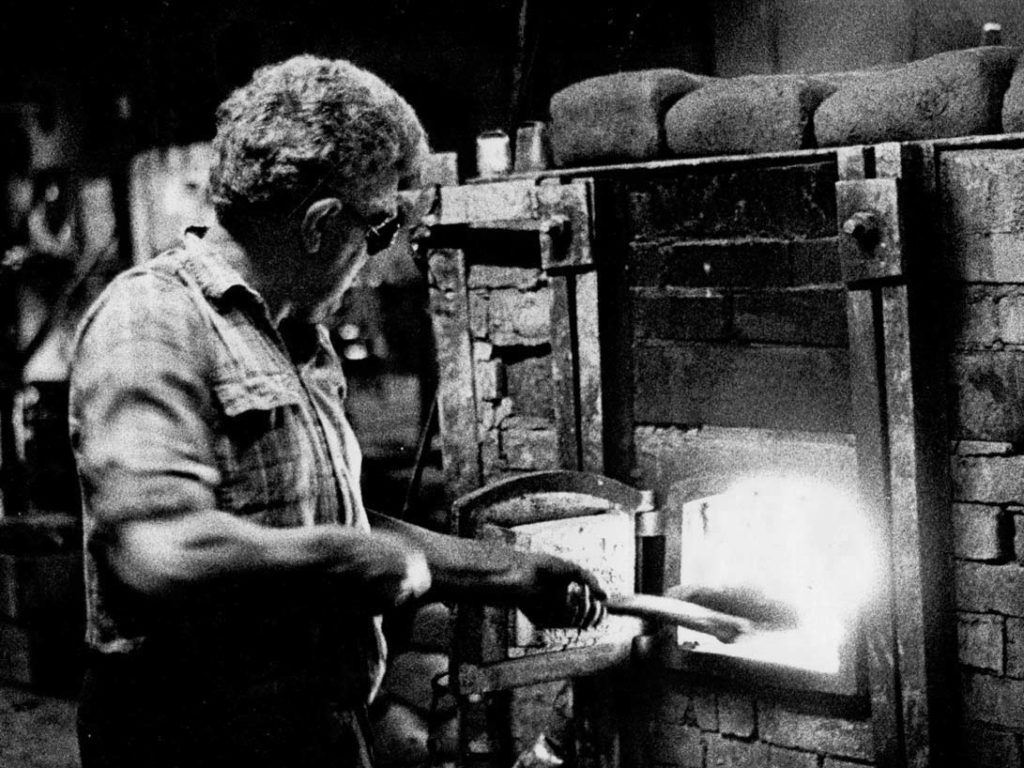
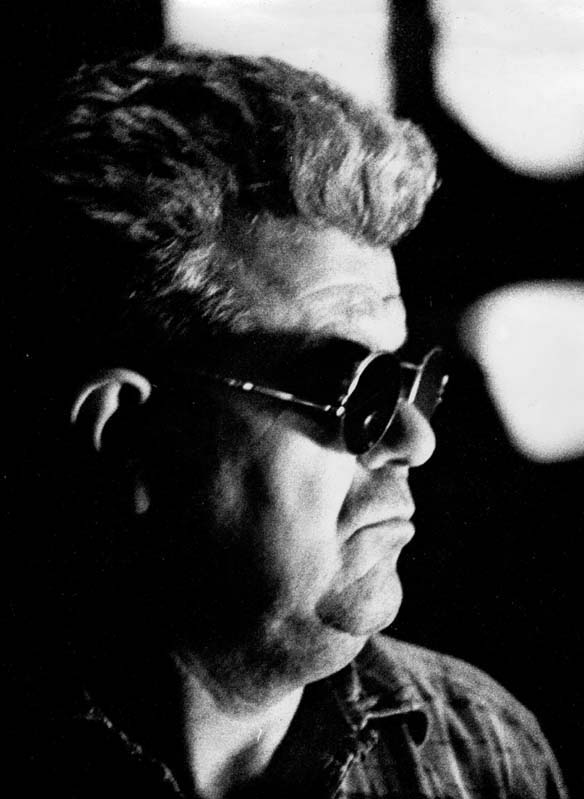
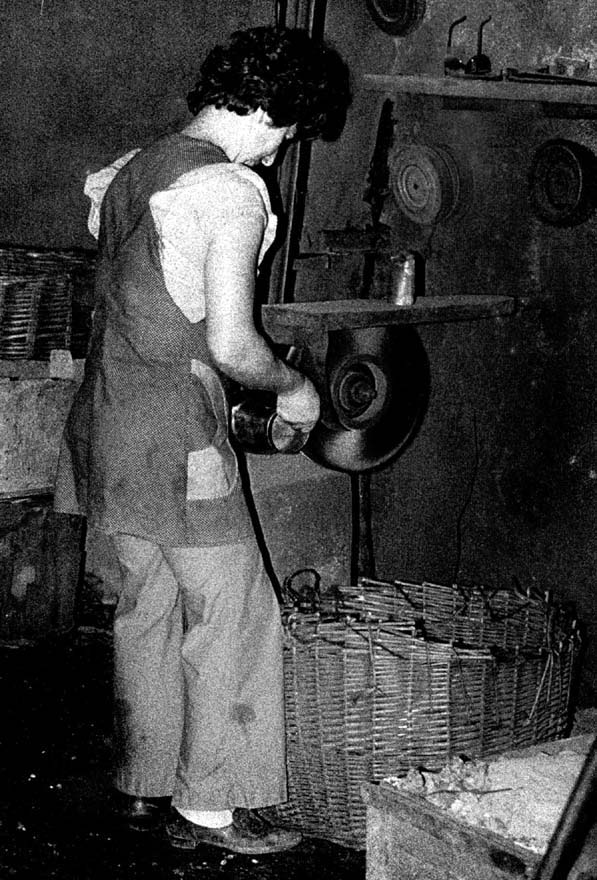
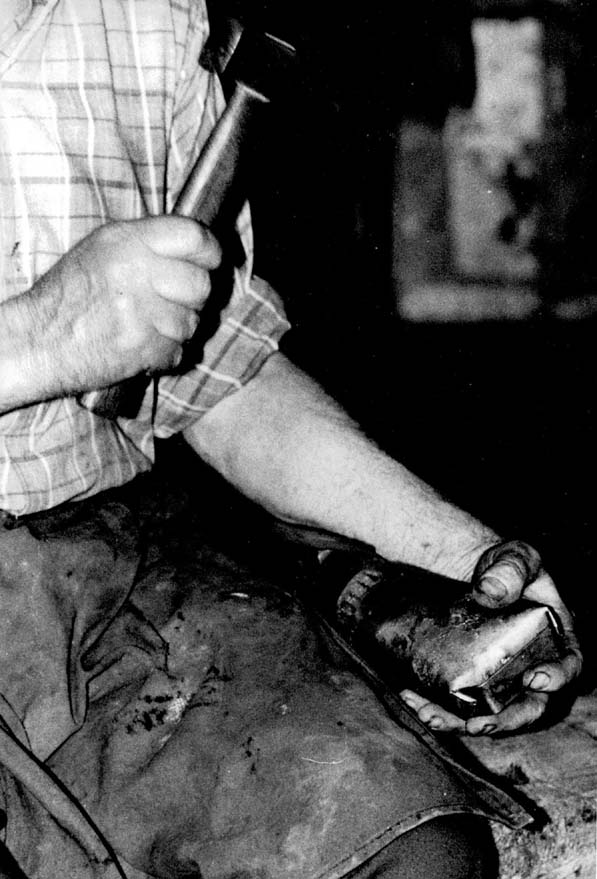
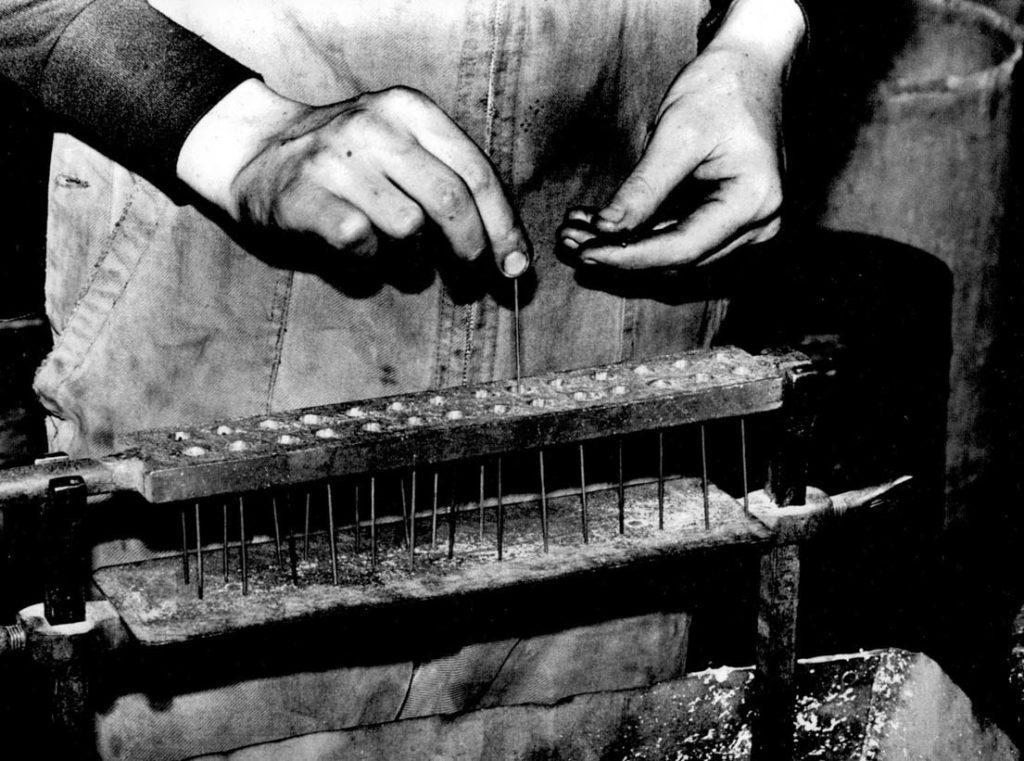
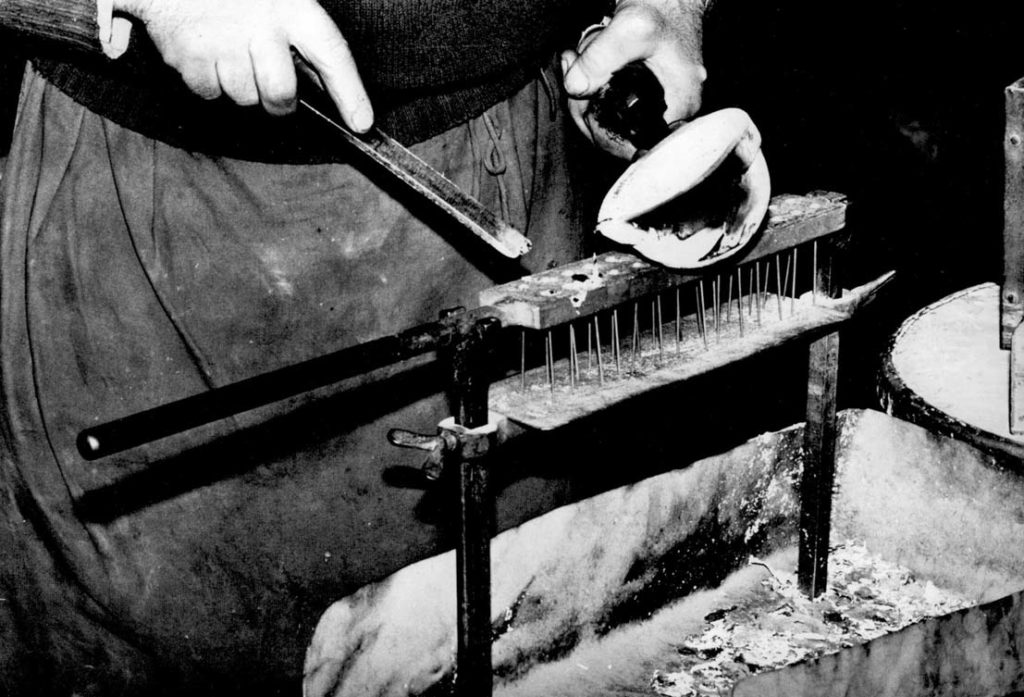
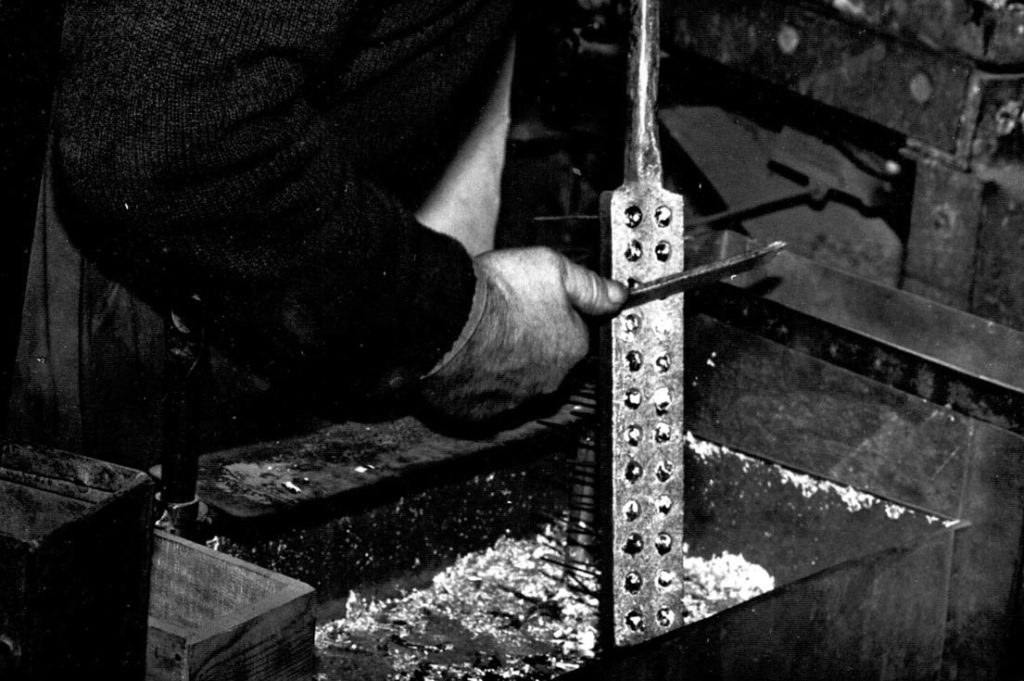
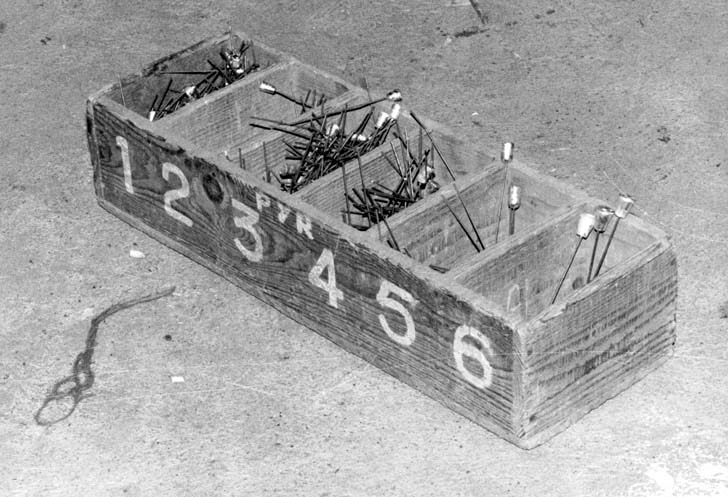
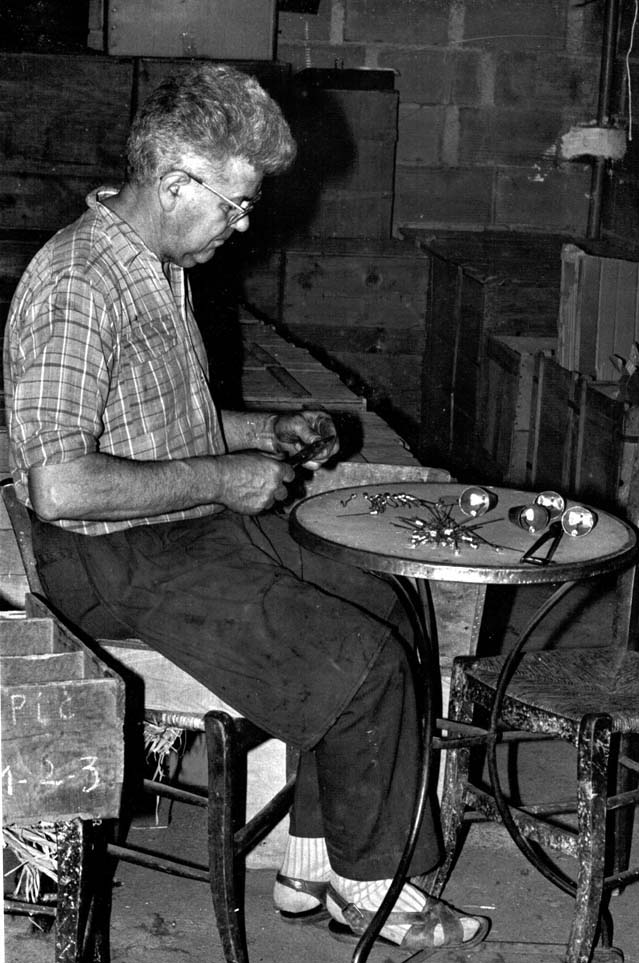
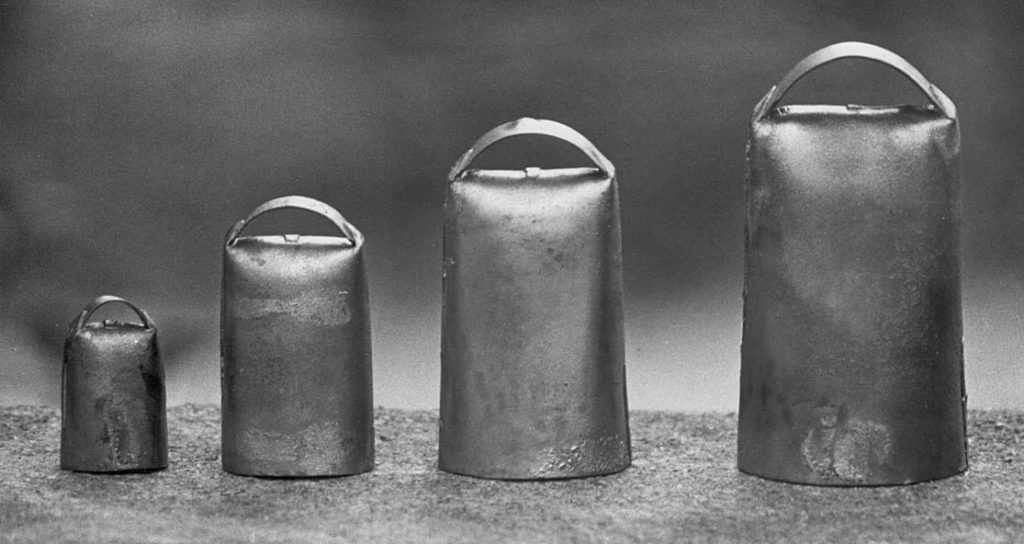
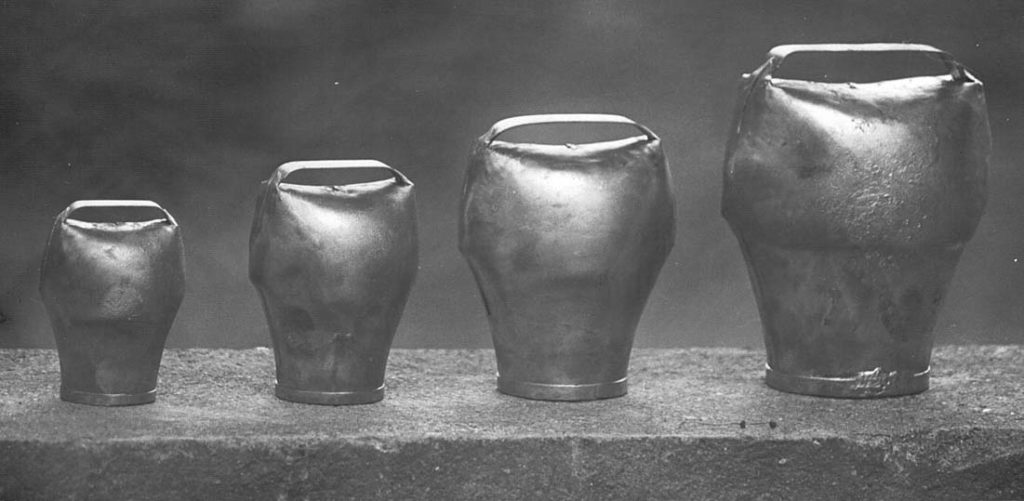
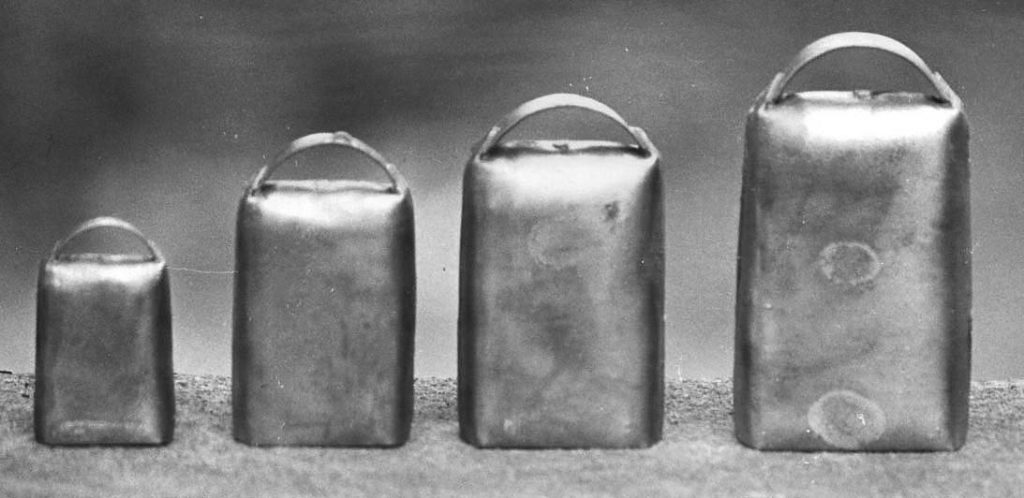
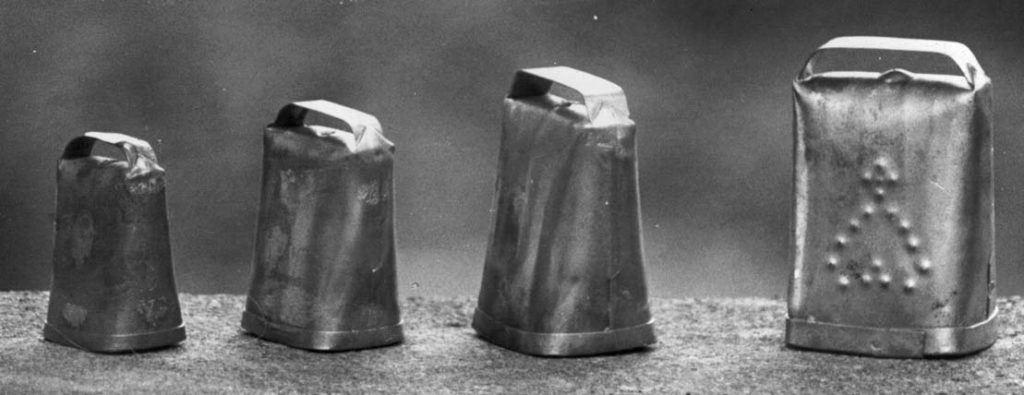
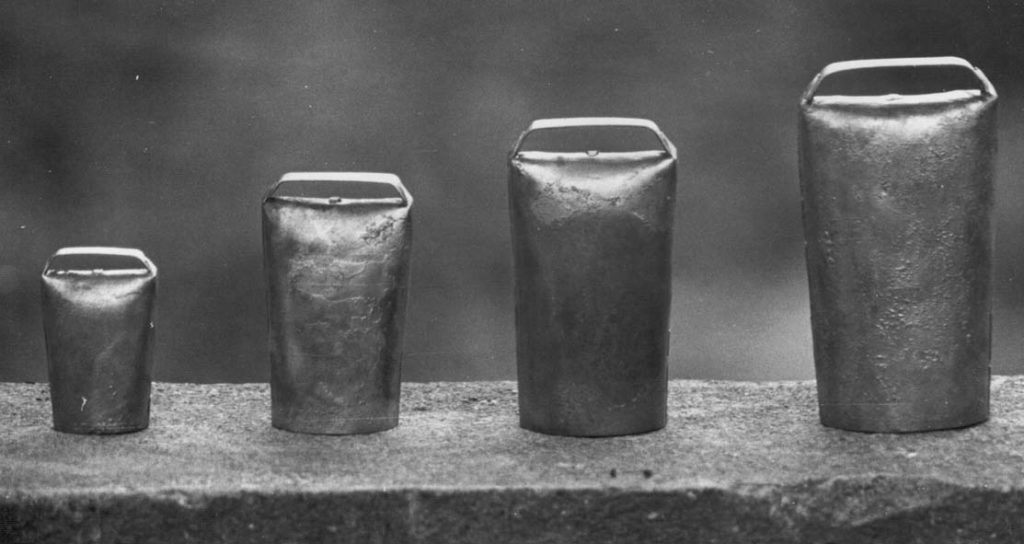
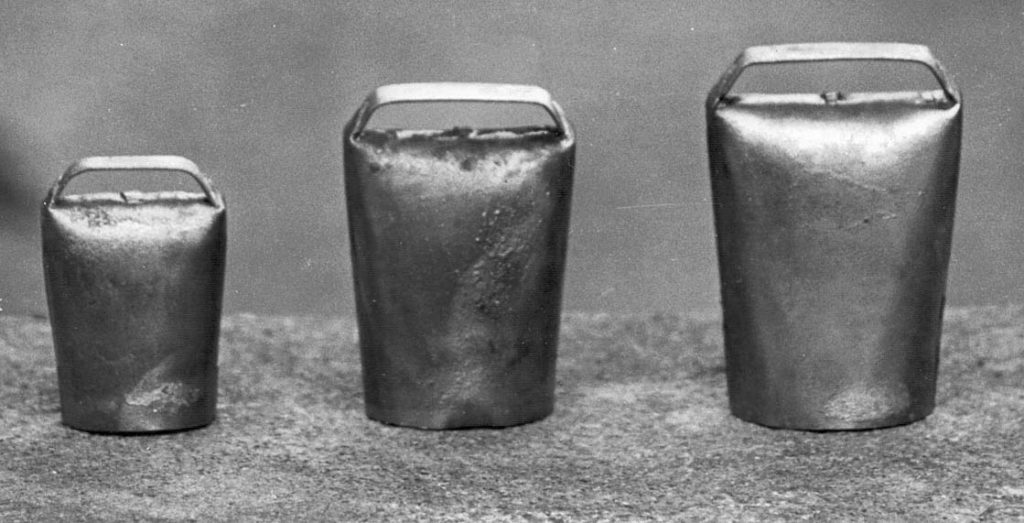
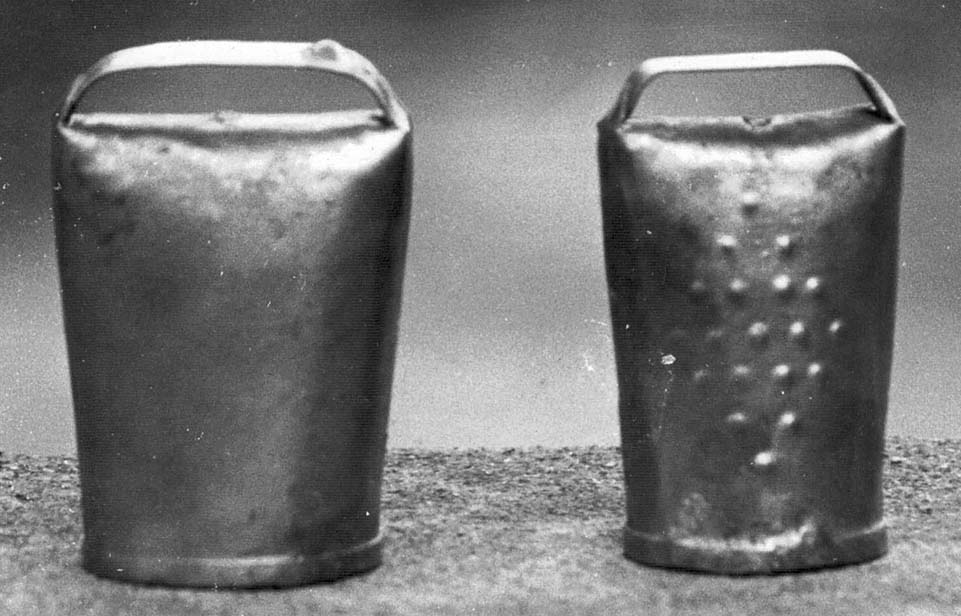
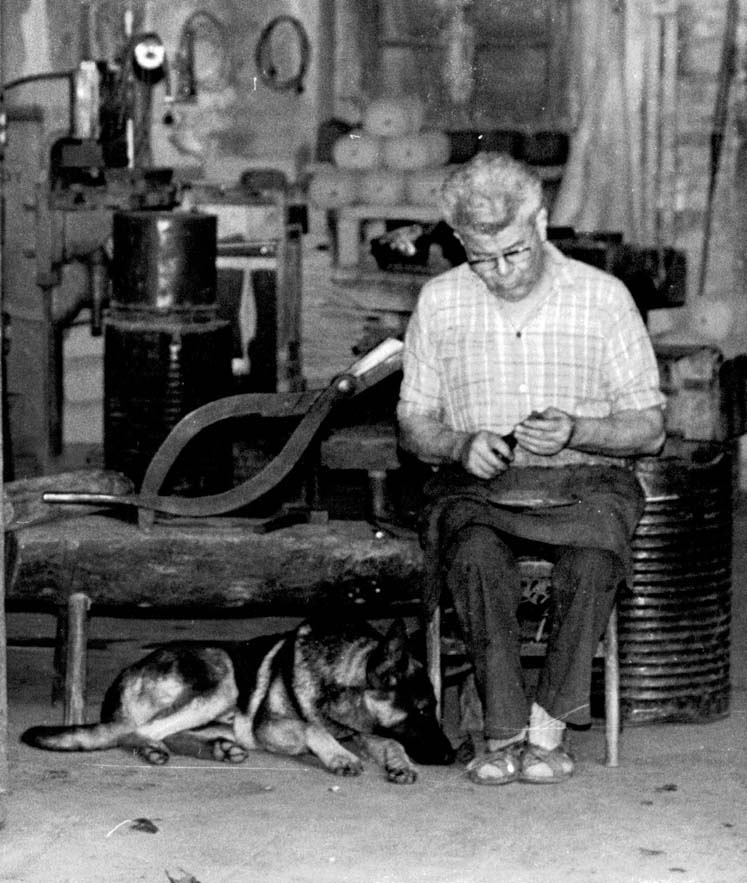
Cliquer pour agrandir les photos
Entretien avec Albert Aubagnac
« Dans la région, il y avait huit fabricants, il y a seulement vingt-cinq ans en arrière ; maintenant, nous sommes moins nombreux, aussi nous continuons à travailler toujours davantage car nous avons beaucoup de demandes. A un certain moment, un prêtre du village voisin avait fait des recherches et pensait que cette industrie aurait été apportée dans le pays par les protestants venus d’Allemagne et chassés pendant les guerres de religion. Elle se serait développée par la suite grâce au charbon qui était exploité tout à côté de Castanet, aux mines de Graissessac. Voici l’anecdote, mais il est possible que ce soit une réalité. A l’heure actuelle, nous continuons à braser nos sonnettes avec le charbon de Graissessac.
En effet, lorsque la sonnaille est façonnée, vient la cuisson qui est la même pour tous les pains, qu’ils soient garnis par des redons, des piques, des piquons ou des pyrénéennes. Nous nous procurons l’argile juste à côté des mines de charbon. Elle est d’abord concassée à un broyeur à marteaux et lorsqu’elle est réduite en poussière très fine, elle passe à un vieux pétrin de boulanger, dans lequel on mélange de la paille et de l’eau ; on obtient une pâte qui nous sert à faire les moules. La paille sert de liant pour que le pain d’argile résiste à 1.500 degrés de chaleur dans notre four. Sans paille, l’argile se fendille et le laiton n’est plus contenu dans le moule ; il se perd dans la braise. En effet, du laiton a été mis à l’intérieur des pains pour l’encuivrage, dans la sonnette et le pain. A la cuisson, on n’a pas d’appareil de contrôle ; c’est à la couleur de la flamme que nous reconnaissons le moment exact pour extraire le moule du four et enlever l’excédent de laiton au plus vite, avant le refroidissement. Environ un quart d’heure – vingt minutes après, le pain est trempé dans l’eau, il est cassé par la suite pour récupérer les sonnettes et l’argile cuite n’est pas récupérable. Le temps de cuisson varie entre une heure et une heure et demie suivant l’épaisseur de la tôle contenue dans les moules. Lorsque les sonnailles sont sorties des pains, on les lave, on les sèche et elles sont poncées pour leur donner un brillant et être plus propres à la vente. Après quoi, elles sont refaçonnées parce qu’au brasage elles sont toujours un peu voilées par la chaleur, et martelées pour obtenir le son exact que veulent les bergers.
A certaines, on met un battant en zinc et à d’autres, à la demande des éleveurs, on peut placer un battant en os. Suivant la région et les coutumes… Pour fabriquer le battant, on utilise un fil de fer qui est placé dans un moule sur lequel on coule du zinc ; après quoi, on renverse presque immédiatement le moule pour que les battants se séparent. Il faut aussi, à l’aide de la pince, faire un cochet au battant pour le placer sur les sonnettes.
La tôle utilisée pour fabriquer les sonnailles nous vient des grossistes situés à Béziers ou Castres, et c’est une tôle qui nous est servie selon nos demandes : de 0,5 mm à 1,2 mm, la feuille de 1 m sur 2 m. Il nous faut toute cette variété d’épaisseur pour obtenir des sons différents dans notre fabrication.
Pour fabriquer une « pique », il faut d’abord partir d’un rectangle découpé qui est ensuite embouti et entaillé. La pique est façonnée au marteau, sur une petite enclume appelée « bigorne » et on lui met un porte-battant et une anse plate. La anse plate est utilisée avec un collier rond en bois – généralement ici du micocoulier, – alors que dans d’autres régions, la anse ronde est employée pour les bestiaux, avec un collier cuir.
La sonnette « redon » est beaucoup plus difficile à faire. Il faut d’abord découper les flancs aux ciseaux à quatre ou cinq endroits différents ; l’emboutissage est plus profond et demande plusieurs passes à la presse à emboutir. Après, il faut faire plusieurs entailles à la cisaille à main pour l’assembler et maintenir un galbe bombé ; on a plus de difficultés à façonner un redon qu’une forme droite comme la pique qui n’a qu’une seule entaille à assembler. En plus de cela, il faut placer une bordure et comme aux autres mettre un porte-battant et une anse. Bien sûr, quand on le met dans l’argile pour l’encuivrage, ça demande beaucoup plus de main-d’œuvre parce que, à cause de sa forme bombée, le nombre de redons dans les pains d’argile est moins important que pour une forme droite.
Les formes de sonnettes sont assez nombreuses : la forme des Pyrénées qui est vendue dans les Pyrénées ; la forme cliquette qui est vendue dans le centre principalement, ainsi que la pique et la clape ; la forme redon qui est vendue généralement dans toutes les régions montagneuses de France. Par contre, la Camargue a une forme un peu spéciale : c’est la sonnette « piquon » ou « clavelas » en tôle généralement épaisse, qui, autrefois, résistait à l’attaque du sel. Enfin, on a le « sonnaillon » qui est vendu pour les chiens de chasse aux armuriers de gros.
On nous dit que les bergers reprochent aux fabricants d’avoir des sonnailles de moins bonne qualité qu’autrefois. Il est exact qu’il nous est bien plus difficile que seulement dix ans en arrière de nous procurer les épaisseurs de tôle correspondant à nos différentes formes de sonnettes. C’est pour cela qu’on arrive moins facilement à obtenir des sons qui, quand même, il faut le reconnaître, étaient bien meilleurs autrefois. Ce n’est pas dû à nous, fabricants ; c’est dû au fait que nous n’avons pas toute la gamme d’épaisseurs nécessaire à notre production.
Pour le choix des sonnettes, chaque berger a ses goûts particuliers : un berger, par exemple, aimera avoir la gamme complète d’une seule variété de sonnettes, alors qu’un autre préfèrera plusieurs gammes. Aux bêtes qui ont deux ou trois ans, par exemple, il mettra des sonnettes beaucoup plus fortes, plus grandes, et qui tranchent le ton avec les autres. Ça, c’est une question de goût.
Quant à l’avenir du métier, il ne s’annonce pas mal à condition que les jeunes s’accrochent et travaillent car la demande est importante. Nous fabriquons en moyenne de trois à trois tonnes et demie de sonnailles par an. En ce qui nous concerne, la fabrique Aubagnac devrait connaître une suite convenable car mon fils aîné, Guy, reprendra l’atelier, aidé peut-être de Michel, le second.
Maintenant, vous savez, les choses peuvent changer. J’ai appris qu’un éleveur du côté de Saint-Martin-de-Londres avait réduit son troupeau de moitié et parquait sur plusieurs kilomètres de garrigue ; le gars qui a parqué n’a plus besoin de sonnettes… Tant que les bergers partiront dans les Pyrénées, par exemple, avec plusieurs milliers de moutons, eux, il leur en faudra bien, sinon, quand ils redescendraient à l’automne, ils en auraient la moitié en Espagne et l’autre moitié au Portugal… Et quoi qu’on dise, pour le mouton, si on veut vraiment du bon lait et de bonnes bêtes de boucherie, il ne faut pas les parquer et les laisser là ; il faut qu’elles aient une nourriture variée… Ce n’est pas en mettant des bêtes dans un champ de luzerne pendant une demi-journée, qu’elles seront plus grasses. Il vaut mieux qu’elles aillent un peu dans la luzerne, un peu là-bas, un peu ici, un peu partout…
Il y a une petite partie de notre production qui est vendue pour les touristes, mais je crois que ça ne vaut pas la peine d’en parler parce que c’est quelque chose qui est vraiment à côté ; ça « coupe un peu le typique de notre travail » et enfin, en voulant dire la réalité, ça n’est pas l’avenir.
L’avenir du métier, c’est vraiment la fabrication de sonnailles sur le plan utilitaire, pour l’éleveur ».
Principales étapes de fabrication de cloches pour ovins
Pour une sonnaille allongée, est utilisée une forme de tôle découpée et entaillée qui est ensuite martelée sur une bigorne. La partie supérieure est perforée à l’aide d’un poinçon et à l’intérieur est fixé le porte-battant. L’anse est remise en place, pincée et coincée entre les deux pointes rabattues de la sonnaille.
Pour une sonnaille bombée, est utilisée une forme découpée différemment qu’il faut passer sur une matrice, à la presse à emboutir, pour l’incurver. La forme est ensuite entaillée, façonnée ; en plus du porte-battant et de l’anse, est fixée une bordure sur la bouche.
La cloche ainsi préparée est soumise à l’encuivrage.
Les sonnailles sont enfermées dans un moule fait d’une pâte d’argile, de paille et d’eau, dans lequel sont introduits des déchets et fragments de laiton. Le paquet est refermé par un couvercle percé d’un trou par lequel s’écoulera l’excédent de laiton après la cuisson.
Les paquets sont mis à sécher puis enfournés et cuits à 1 500 degrés, pendant environ une heure et demie. Le moule vitrifié est retiré du four, refroidi et brisé. Les sonnailles cuivrées qui en sortent sont ensuite lavées, brossées pour leur donner un brillant, martelées pour obtenir le son et équipées d’un battant en zinc ou en os.